Stick welding (SMAW), a stalwart of the industry, remains a popular choice for its versatility and ease of use. Unlike other techniques, it utilizes a consumable electrode coated in flux. This flux generates a protective gas shield as it burns, preventing contamination of the weld pool. Despite advancements in welding technology, SMAW’s simplicity and effectiveness continue to make it a reliable go-to process across various applications. ARC Welding Fabrication is one of the best welding company in Houston to hire for any welding projects.
History of Stick Welding
Stick welding has a rich history dating back to the late 19th century when Russian inventor Nikolay Benardos first patented the process. Since then, it has evolved significantly, with improvements in electrode composition, welding machines, and safety gear.
Advantages of Stick Welding
Flexibility of stick welding
One of the key reasons for the widespread use of stick welding is its flexibility. It can be used on a variety of metals, including steel, stainless steel, cast iron, and aluminum, making it suitable for diverse applications.
Lightness Stick welding
Stick welding equipment is relatively compact and portable compared to other welding methods. This makes it ideal for outdoor or remote welding jobs where access to electricity may be limited.
Cost-effectiveness
Another advantage of stick welding services is their affordability. The equipment and consumables required for stick welding are generally more economical compared to other welding processes, making it accessible to hobbyists and professionals alike.
Equipment Needed for Stick Welding
To perform stick welding, you’ll need the following equipment:
Welding Machine for Stick welding
A stick welding machine, also known as an arc welder, is the primary tool used to create the weld. These machines come in various sizes and power outputs to suit different welding applications.
Electrodes
Electrodes, or welding rods, are coated in flux and come in different types and sizes depending on the metal being welded and the welding technique used.
Safety Gear
Safety gear is essential when stick welding to protect against burns, electric shock, and harmful fumes. This includes welding gloves, a welding helmet with a protective lens, and flame-resistant clothing.
Techniques of Stick Welding
Mastering stick welding requires understanding and practice of various techniques, including:
Arc Length
Maintaining the correct arc length between the electrode and the workpiece is crucial for a successful weld. Too long of an arc can cause spatter and an unstable arc, while too short of an arc can lead to sticking and slag inclusion.
Electrode Angle
The angle at which the electrode is held relative to the workpiece affects the weld bead shape and penetration. Experimenting with different angles can help achieve the desired results.
Travel Speed
Controlling the travel speed of the electrode along the joint is essential for maintaining proper heat input and achieving good fusion. Too fast of a travel speed can result in insufficient penetration, while too slow can lead to excessive heat buildup and distortion.
Common Applications of Stick Welding
Stick welding finds use in a wide range of industries and applications, including:
Construction
Stick welding is commonly used in construction for joining structural steel beams, columns, and plates, as well as for repairing metal structures and equipment on-site.
Automotive Repair
Automotive technicians often rely on stick welding for repairing vehicle frames, exhaust systems, and other metal components due to its accessibility and versatility.
Shipbuilding
In shipbuilding, stick welding is used for fabricating and repairing metal hulls, decks, and other structural components due to its ability to withstand harsh marine environments.
Challenges of Stick Welding
While stick welding offers many benefits, it also presents some challenges, including:
Limited Positioning
Stick welding can be challenging in confined spaces or when welding in overhead or vertical positions due to the nature of the process and the need to maintain a consistent arc.
Slag Removal
The flux coating on stick welding electrodes produces slag, which must be removed after welding to reveal the finished weld bead. This additional step can be time-consuming, especially on large or intricate welds.
Tips for Successful Stick Welding
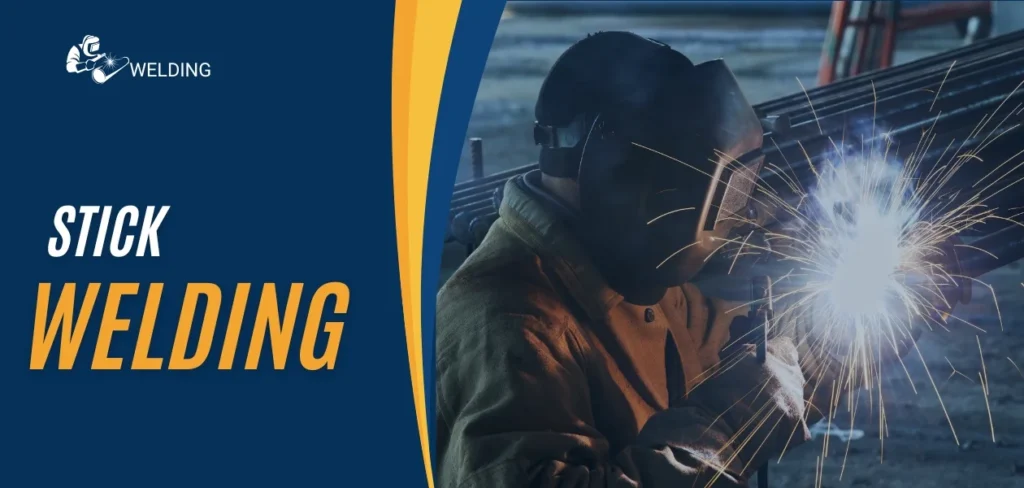
To improve your stick welding skills, consider the following tips:
Clean Surface
Ensure the workpiece is clean and free of rust, paint, and other contaminants before welding to achieve better weld quality and penetration.
Proper Amperage Setting
Adjust the welding machine’s amperage settings according to the electrode diameter and material thickness for optimal weld results.
Practice and Patience
Stick welding requires practice and patience to master. Take the time to experiment with different techniques and settings to improve your skills over time.
Conclusion
In conclusion, stick welding remains a widely used welding process due to its versatility, portability, and cost-effectiveness. By understanding the equipment, techniques, and common applications of stick welding, you can achieve quality welds in various metalworking projects.
Unique FAQs
Is stick welding suitable for beginners?
- Yes, stick welding is beginner-friendly and a great way to learn the fundamentals of welding.
Can stick welding be used for aluminum?
- While stick welding can be used for aluminum, it is less common and typically requires specialized electrodes and equipment.
How do I choose the right electrode for stick welding?
- The choice of electrode depends on factors such as the metal being welded, the welding position, and the desired weld characteristics. Consult with a welding supplier or reference welding guides for guidance.
What safety precautions should I take when stick welding?
- Always wear proper safety gear, including welding gloves, a helmet with a protective lens, and flame-resistant clothing. Ensure adequate ventilation to prevent exposure to welding fumes.
Can stick welding be used underwater?
- Yes, stick welding can be adapted for underwater welding applications using specialized equipment and techniques.